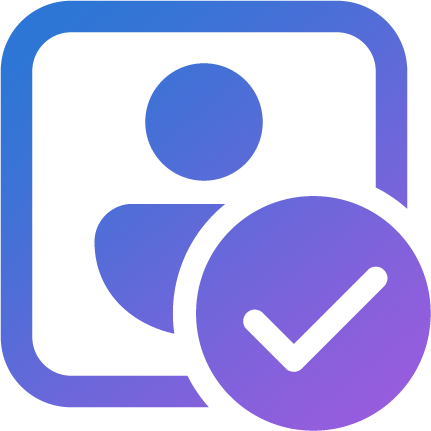
Microsoft Copilot opportunity to impact key functional area KPIs
Review our KPI overviews and view additional scenario details.
Product time to market
Use Copilot capture customer needs and then support coordination of product development activities.
KPI — Product time to market
Use Copilot capture customer needs and then support coordination of product development activities.
How Microsoft Copilot can help improve product time to market
Boost productivity
- Rapidly find information
- Diagnose problems faster
- Check for similar issues and resolutions
- Quickly send follow-up communications
Improve your data
- Use Copilot Studio for secure data retrieval from existing systems
- Quickly analyze trends
- Generate informative charts
- Create strategy presentations
Roles
- Product Designer
- Process Engineer
Microsoft AI solutions
- Microsoft 365 Copilot
- Copilot Studio
Employee turnover
Retain critical plant and headquarters staff by improving the work/life balance of all workers by simplifying overhead tasks. Improve skilling to provide more growth opportunities and increase internal hiring.
KPI — Employee turnover
Retain critical plant and headquarters staff by improving the work/life balance of all workers by simplifying overhead tasks. Improve skilling to provide more growth opportunities and increase internal hiring.
How Microsoft Copilot can help employee turnover rates
Improve quality of internal materials and processes
- Improve job descriptions for further role clarity
- Improve company meetings with summarization and recap
- Completely focus during the meeting
Improve employee collaboration
- Use Copilot in Loop to drive internal collaboration
- Use Copilot to surface ice breakers
Create internal feedback loop
- Draft employee surveys
- Analyze surveys to gain valuable insights into what makes employees happy or areas that need improvement within the organization
Roles
- Human Resource Manager
- Production Manager
Microsoft AI solutions
- Microsoft 365 Copilot
- Copilot Studio
Customer satisfaction
Improve customer service performance with tailored LLMs for higher first-time call resolution. Improve customer communications whether through improved writing or improved call scripts.
KPI — Customer satisfaction
Improve customer service performance with tailored LLMs for higher first-time call resolution. Improve customer communications whether through improved writing or improved call scripts.
How Microsoft Copilot can help customer satisfaction
Incorporate feedback
- Rapidly analyze customer feedback
- Quickly create recommendations
- Swiftly update scripts and processes
- Create communications to socialize the changes
Enhance customer loyalty
- Better understand customers
- Resolve issues on the first call
- Limit the need for escalations
- Anticipate emerging trends
Roles
- Customer Service Manager
- Customer Service Agent
Microsoft AI solutions
- Microsoft 365 Copilot
- Copilot for Service
Scrap rate
Quickly identify quality issues by accessing and analyzing quality logs. Reduce the cost of any recall programs that are required with effective management and tailored responses.
KPI — Scrap rate
Quickly identify quality issues by accessing and analyzing quality logs. Reduce the cost of any recall programs that are required with effective management and tailored responses.
How Microsoft Copilot can help minimize scrap rate
Speed problem resolution
- Rapidly find information
- Diagnose problems faster
- Check for similar issues and resolutions
- Quickly send follow-up communications
Speed data analysis and reporting
- Quickly analyze trends
- Generate informative charts
- Create strategy presentations
Roles
- Production manager
Microsoft AI solutions
- Microsoft 365 Copilot
- Copilot Studio
Supply chain performance
Use AI to generate evaluation criteria for new materials and suppliers. Review contracts to make the most effective deals and use AI analysis to evaluate supplier performance.
KPI — Supply chain performance
Use AI to generate evaluation criteria for new materials and suppliers. Review contracts to make the most effective deals and use AI analysis to evaluate supplier performance.
How Microsoft Copilot can help supply chain performance
Speed data analysis and reporting
- Quickly analyze trends
- Generate informative charts
- Create strategy presentations
Roles
- Supply Chain Manager
Microsoft AI solutions
- Microsoft 365 Copilot
- Copilot Studio
Minimize production downtime
Use Copilot to analyze information from manufacturers apps to predict and prevent equipment failures, manage inventory levels and identify training that can help staff keep machines operating.
KPI — Minimize production downtime
Use Copilot to analyze information from manufacturers apps to predict and prevent equipment failures, manage inventory levels and identify training that can help staff keep machines operating.
How Microsoft Copilot can help minimize production downtime
Speed problem resolution
- Rapidly find information
- Diagnose problems faster
- Check for similar issues and resolutions
- Quickly send follow-up communications
Speed data analysis and reporting
- Quickly analyze trends
- Generate informative charts
- Create strategy presentations
Roles
- Maintenance technician
- Production manager
Microsoft AI solutions
- Microsoft 365 Copilot
- Copilot Studio
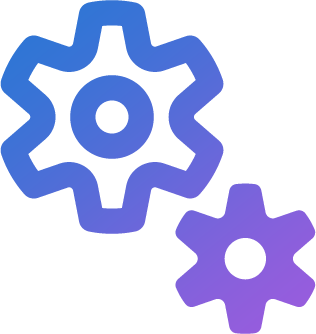
Transform Manufacturing processes
Key processes | Before AI | Using AI |
---|---|---|
Accelerate product development and engineering through generative AI | Product teams spend substantial time refining and optimizing product designs to meet performance, cost, and production requirements. With AI, they can enhance innovation, research, and design with AI support across the entire innovation lifecycle. This support includes using AI to provide ideas, feedback, and intelligently mine customer behavior and interactions for new products. Once products are released companies are increasingly turning to AI for assistance with product support including AI product assistants. | AI can help manufacturers respond to customer requests for new products and even predict future customer needs for products that do not exist today. AI can help customers translate their requirements into product designs and prototypes in minutes. With AI engineers they get assistance with research, ideation, and collaboration to quickly generate innovative solutions. With AI product teams can get assistance with research, ideation, and collaboration to quickly generate innovative solutions. Improve product development from ideation to launch. |
Optimize supply chain and logistics management | AI can significantly enhance supply chain management for manufacturers by improving visibility and efficiency. It enables real-time monitoring and predictive analytics, allowing manufacturers to anticipate and mitigate potential disruptions. AI also optimizes inventory management and demand forecasting, ensuring that resources are allocated effectively. Additionally, AI-powered automation can streamline processes, reducing operational costs and increasing overall productivity. | Procurement teams can use Copilot Chat to assist with research and collaboration to find new suppliers. Automate freight invoice processing and error checking to reduce shipping costs. Set production schedules based on sales and inventory From assessment to transition plans Copilot can help with supplier management Improve the RFP process from creating the RFP to awarding the contract Using Copilot for contract lifecycle management |
Transform factory operations with real-time data access and AI agents | Manufacturers dedicate substantial time to optimizing their processes to ensure efficiency and streamline operations. AI-enabled employees can leverage real-time access to information to help ensure uptime and prevent defects that slow production. Use AI to automate communications and scheduling through data analysis. AI can assist factory and field workers with information and reporting to speed tasks and keep the focus on production. AI can be used to shorten manufacturing cycles, while ensuring higher-quality outputs and faster, more efficient delivery. AI integration helps manufacturers build more agile and responsive operations, driving innovation and competitiveness. | Deliver critical information and expert assistance to workers during maintenance activities to reduce downtime. Use an agent to help improve factory operations and OEE Use the Factory Safety Agent to help avoid incidents Help field engineers solve customer issues Support maintenance activities to reduce downtime. Streamline the process from early detection to effective communications Analyze equipment data and maintenance schedules Plant workers can complete a variety of tasks more easily with Copilot |